Powder Recovery Cyclones
Application of 'Uni-Dust Systems' in
'Powder Containment'
Air/solids cyclone technology provides an effective and very efficient solution for the separation and collection of powders in dust extraction applications.
Leading the way in the control of excess dust from powder filling machines, the pioneering technology behind the Hanningfield filter-less, high efficiency Uni-Dust Powder Recovery Cyclone offers the ultimate in powder containment solutions.
Manufactured in 316L stainless steel, the Uni-Dust cyclone is a hygienic method of capturing excess dust in the controlled environment of the process room.Uni-Dust is the ideal solution for the capture of waste material in powder processing.
The equipment is designed to be retrofitted to any dust generating plant; process validation is not effected, making it ideal for both new and existing processes. In-line with cGMP the Uni-Dust makes loss reconciliation a simple matter.
- Profile
- Traditionally, waste material from powder filling equipment such as tablet presses and capsule filling machines is piped away to a central dust collector located in a plant room. This process results in a cocktail of various powders being stored in an uncontrolled area causing potential environmental damage and operator exposure.
The Uni-Dus cyclone separates the solids from the clean air, typically apturing 95-99% of excess powder in a collection pot, the air is then passed through an optional “police” HEPA filter which increases system efficiency to 99.99% before the clean rather than contaminated air flows to the normal dust extraction unit.
- Features
- •Hygienic stainless steel construction
•Filter-less design
•No moving parts
•‘Easy clean’ hygienic design
•Complete ‘safe change’ facility available
•External HEPA police filter
•Compact, space-saving design
•Designed & Manufactured in the UK
•Keep waste material in the process room
•Improve the working environment by creating safer and more hygienic conditions
•Reconcile batch losses
•Improve GMP and site safety standards - Technical Specifications
- •Material of Construction: Stainless steel (304 or 316)
•Powder Capture Rate: Typically 95-99%
•Height: Ranges from 475 to 1240mm
•Body diameter: Ranges from 100 to 300mm
•Version: Mobile or stationary version available
•Explosion Protection: ATEX or Non-ATEX version available - Typical Applications
- •Capture excess powder from tablet presses
•Capture excess powder from capsule filling machines
•Capture excess powder from sachet filling machines
•Capture excess powder from inhaler filling machines
•Capture excess powder from tablet drills
•Capture excess powder from pharmaceutical processing applications
•Capture excess powder from food processing applications
•Capture excess powder from chemical processing applications - Gallery
- See it in Action!
-
Click to download in FLV format (13.02MB)
What is the Uni-Dust Cyclone?
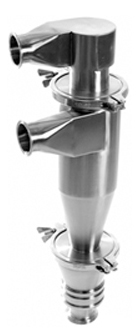
The filterless Uni-Dust is a highly efficient cyclone made from stainless steel. The cyclone has been specially designed for applications in the process industries where powder and dust is often generated and lost.
The fundamental idea of the equipment is to capture as much powder as possible that would otherwise have been lost to the filters.
How Does it Work?
How Does it Work?
The cyclone separates the solids from the clean air, typically capturing at least 95% of excess powder in a collection pot. The air is then passed through a "police" HEPA filter which increases system efficiency to 99.99% before the clean air flows to the normal dust extraction unit.
By capturing at least 95% of the excess powder in a collection pot, it becomes possible to safely dispose of excess powder, or even to reintroduce it to the front end process.
Why Do I Need It?
As with most things, prevention is better than cure. The Hanningfield Uni-Dust cyclone adopts this principle by offering a best-practice solution to the problem of handling excess powder, typically capturing over 95% of all waste on standard pharmaceutical, food and chemical powders.
The loss of excess powder from a process has always been a major issue for engineers – whether a process engineer is losing powder from a tablet press during compression or a line manager is losing powder from a sachet filling machine – the principle is the same, powder is being lost.
Often, existing dust extraction systems cause downstream filters to become blinded or a cocktail of various powders to build up in the filter of the central dust extraction system. If either filter becomes blocked, this can be expensive and time-consuming to change.
Learn More
The equipment is designed to be retrofitted to any dust generating plant as process validation is not affected, making it ideal for almost any new or existing process.
If you have any questions in this regard, or wish to place an order for this equipment please click here.
Pharmaceutical Powder Processing
Pharmaceutical Powder Processing
This well established principle offers many major benefits for powder containment. However, generally, the use of air/solids cyclone separators in pharmaceutical processing environments has been virtually non-existent until now.
The main benefits for many common pharmaceutical powder processing applications is that by using filter-less powder transfer, there are no moving parts and no loss in performance as a result of pressure drops caused by clogged filters contaminated with product.
It was while working on a project for a major pharmaceutical client several years ago that Hanningfield Process Systems discovered the many benefits of cyclone technology. The client needed to ensure that waste material from a high speed capsule filling machine could be arrested and recovered within the process room.
The early designs of this system employed the use of a hybrid design generally based upon established vacuum conveying techniques with which Hanningfield had gained much experience while manufacturing its own Uni-Vac Vacuum Conveying System.
Although the original design provided a solution to the customers’ problem of powder containment, it soon became apparent that the system would greatly benefit from the use of filter-less air/solids cyclone technology. Hanningfield invested in an all new design and development project which incorporated as many GMP desirable options as possible. Based around established cyclone principles for air and solids separation, the design put much emphasis on an easy-clean hygienic construction with an option of a full safe-change facility for the powder collection receptacle.
A further benefit of the filter-less design meant that filter cleaning by compressed air is no longer necessary, further simplifying the system and improving the integrity of the design.
Powder Recovery System
Powder Recovery System
The benefits of the Uni-Dust Powder Recovery System are of great significance to any powder processing application requiring the highest levels of containment and efficiency. As waste material is retained within the confines of the process room it ensures that centralised dust collectors are able to operate in a clean condition for longer than average, thus saving money by reducing the number of filter changes. During government MHRA and FDA inspections, the added benefit of batch loss reconciliation also provides evidence of powder loss control.
The Uni-Dust filter-less cyclone is of compact design which allows the unit to be easily installed within existing process facilities such as tablet compression suites and high speed capsule filling suites. It can also be used with existing ‘in-house’ dust extraction systems or alternatively, supplied with a dedicated vacuum unit supplied and installed by Hanningfield’s own technicians. The supply of an optional police HEPA filter, guarantees that any small amounts of carry-over that are not trapped by the cyclone, are arrested before reaching the vacuum source. The specially designed all stainless steel construction HEPA unit, can be installed in the process room wall creating a neat unobtrusive installation with easy access within the controlled environment of the process room.
Numerous systems are now in full operation both the UK and the USA and the most recent installation at one of the UK’s leading pharmaceutical manufacturers, has provided an essential part of the closed system for containment and safe recovery of excess material.
Download Brochure:
Powder Recovery Cyclones (Uni-Dust Series)